РЕЗИНОВЫЕ КОЛЬЦЕВЫЕ УПЛОТНЕНИЯ предназначены для уплотнения неподвижных соединений, в тех случаях, когда требуется обеспечить герметичность одновременно с точным и мощным креплением сопрягаемых деталей. К величайшему сожалению, принцип работы и назначение этого вида уплотнений практически неизвестен ремонтникам. Иначе как объяснить поголовные попытки обеспечить герметичность стыков подмазыванием герметика под резиновые кольца?
Итак, каким образом работает резиновое уплотнительное кольцо? Резиновыми кольцами круглого сечения уплотняют всевозможные соединения типа трубопроводов и плоские стыки. Принцип работы кольца всюду одинаков, поэтому для краткости рассмотрим уплотнение плоского стыка. Таких узлов в моторах множество: водяная помпа на 5 и 6 цилиндровых VW, соединение вакуумного насоса с генератором, крышка топливного насоса высокого давления и множество других узлов. Резиновое кольцо размещается в канавку, проточенную или профрезерованную в корпусе (рис. 11а). При этом обязательно должно соблюдаться два условия:
- резиновое кольцо обязательно должно выступать над плоскостью корпуса примерно на 0,5 мм (рис. 11б);
- канавка должна быть такой ширины, чтобы после обжатия кольцо могло раздаться в пределах канавки; иначе уплотнение работать не будет (рис. 11в).

Рис. 11. Уплотнения с помощью резинового кольца
При возникновении в полости корпуса избыточного давления, среда (топливо, масло, газ) по шероховатостям поверхностей проникает в канавку и деформирует кольцо (рис. 11г), что способствует улучшению уплотнения. И чем давление выше, тем качественнее уплотнение. Если же кольцо от старости потеряло эластичность и деформировалось, попытки устранить протечку с помощью герметика только усугубляют ситуацию.
Слой герметика выдавится даже самым малым давлением, а кольцо, и без того просевшее, получит еще меньший обжим. Ассортимент выпускаемых отечественной промышленностью колец круглого сечения очень широк, а зарубежной — вообще необозрим, так что проблема отсутствия деталей на сегодняшний день не очень актуальна. Кроме того, довольно просто изготовить резиновые кольца, для работы в статических условиях, склеив их из резинового шнура (фирма LOCTITE выпускает даже специальный набор для склеивания любых колец). Ну и уж если ситуация напряженная, и покупка колец невозможна, существует еще два способа решения проблемы. Первый — изготовить подкладку под резиновое кольцо, чтобы увеличить его выступание над корпусом (рис. 11д).
Второй — изготовить необходимое кольцо. Все что для этого надо: сырая масло-бензостойкая резина, токарный станок и сушильный шкаф или на худой конец бытовая духовка. Прессформа и готовые кольца показаны на рис. 12. Прессформу по вашим эскизам изготовит любой токарь. Важно только, чтобы ее внутренняя поверхность была хорошо отполирована. Закладывать нужное количество сырой резины вы научитесь с 2-3 попыток. Ну а завулканизировать изделие при температуре 140 градусов в течение 20 мин уж и совсем не фокус.
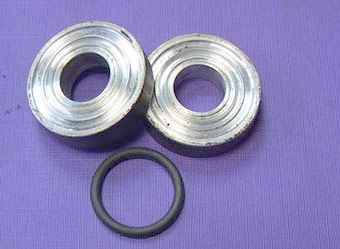
Рис. 12. Прессформа для изготовления резинового кольца
УПЛОТНИТЕЛЬНЫЕ ШАЙБЫ предназначены для уплотнений всевозможных резьбовых уплотнений. Изготавливаются, как правило, из меди (многоразовые) и из чистого алюминия (одноразовые). Медные шайбы, как для первичного, так и для повторного использования должны быть отожжены, для придания металлу мягкости и податливости. Отжиг осуществляется нагревом любым способом до светло-красного цвета, после чего шайба немедленно погружается в воду. Медь после этой процедуры приобретает розовый цвет и становится столь мягкой, что шайбы можно гнуть пальцами.
Казалось бы, что уж может быть проще уплотнений шайбами? Однако неправильный выбор внутреннего диаметра шайбы или ее высоты может привести к неплотности соединения (рис. 13). И что уж совсем поразительно, так это то, что мне доводилось видеть попытки исправить неправильный подбор шайбы герметиком.

Рис. 13. Уплотнение шайбами
Еще одной частой ошибкой является постановка двух медных шайб одновременно. Часто приходилось сталкиваться с таким решением, и всегда такие соединения потели.
Еще одним частным случаем уплотнения шайбами является уплотнение форсунок в головке блока. В очень многих моторах (VW, MB, Ford) применяются специальные уплотнительные (они же пламягасящие или теплоотводящие) шайбы (рис. 14), которые можно только купить и никаких иных вариантов тут не существует.

Рис. 14. Шайбы под форсунки
Во многих моторах (TOYOTA, NISSAN, OPEL, FIAT) для уплотнения форсунок применяются штампованные шайбы, а так же так называемые “дутыши” (рис. 15).

Рис. 15. Дутые шайбы под форсунки
Практика показывает, что эти виды шайб с успехом могут заменять друг друга. В условиях некоторых сервисов имеющих трудности со снабжением, изготовление таких шайб не представляет никаких трудностей. На рис. 16 показана прессформа, в которой автор в 80-90 годах назад изготавливал уплотнительные шайбы.

Рис. 16. Прессформа для изготовления дутых шайб
ШЛАНГИ — казалось бы, что тут может быть хитрого? Однако совсем не редка ситуация когда в охлаждающую жидкость попадает масло или снаружи на них протекает топливо. Резина набухает, и размер шланга становится существенно больше, чем у патрубка (рис. 17).

Рис. 17. Деформированный патрубок
Единственный способ ремонта — замена шланга. Никаких иных решений тут не может быть. Разбухшая резина теряет связь с кордом, шланг теряет прочность. В любой момент он может лопнуть с самыми печальными последствиями для мотора и кошелька хозяина (рис. 18).

Рис. 18. Поврежденный патрубок
Но не тут то было! Накладывают мощный хомут, а то и пару и под шланг набивают что? Правильно! Все тот же герметик! Причем в недопустимости намазывания герметика на соединения шлангов с патрубками мне не всегда удавалось разубедить даже очень приличных инженеров. Ответ — “ты абсолютно прав, но я знаю, как надо намазать”. И мажет, как щедрая мама масло на бутерброд дитятке. Пока этот герметик не вытащишь у него из канала закипевшего и заклинившего мотора, не переубедишь. Выход из положения только один — заменять шланги. Конечно лучше на новые, родные. Однако иногда кажется, что это дорого, иногда просто не купить. Для ремонтных целей выпускается широкая гамма специальных шлангов со стальной спиралью внутри (рис. 19).

Рис. 19. Комплект ремонтных патрубков
Конструкция шлангов позволяет придавать им любой изгиб. Цена их невелика и купить их теперь не очень сложно. Кроме того, для этих же целей могут быть применены фрагменты отечественных шлангов от всевозможных автомобилей и тракторов. Ассортимент их весьма широк, и с помощью выточенных переходников можно решить почти любую проблему.
ГЕРМЕТИКИ — бич и спасательный круг авторемонтников. Без них сегодня невозможно представить ни один двигатель, но и несть числа моторам, загубленным неумелым применением герметиков. Более четырех лет назад ко мне попал в ремонт мотор магистрального грузовика RENAULT MAGNUM, у которого в мясо были перемолоты все вкладыши, и не подлежал восстановлению коленвал. И все это через сто километров после предыдущего ремонта мотора. Затраты на ремонт этого мотора даже сейчас вспоминать страшно. Причина? Слесари при ремонте, для чего-то решили уплотнить заглушки масляных каналов, подводящих смазку к коренным опорам, кроме медных шайб еще и герметиком.
Да еще и не пожадничали... Герметик этот
(опять мой ненаглядный рыжий) мы обнаружили потом всюду, и в щелях разорванных вкладышей и даже в каналах подвода смазки к верхней головке шатуна.
Меня можно заподозрить в рекламе продукции LOCTITE, но я просто много лет назад нашел для себя и оценил качество продукции этой фирмы. А заниматься изучением рынка и проверкой качества и удобства пользования продукции иных производителей у меня нет ни времени, ни желания. Ведь есть же люди, которые предпочитают ездить только на Мерседесах.
Итак, герметики (неважно какого производителя) в зависимости от назначения подразделяются на твердые (обеспечивающие прочное сцепление сопрягаемых поверхностей), эластичные и нетвердеющие (позволяющие легко разъединять сопряжения). Безусловно, герметики для авторемонта должны быть масло-бензостойкими.
Известные мне герметики LOCTITE специально разработаны для ремонта двигателей и совершенно не меняют своих свойств от контакта с техническими жидкостями. Единственный их недостаток — высокая цена. Однако высокая цена с лихвой окупается качеством.
Твердые герметики (типа Ultra Black) имеют, пожалуй, наиболее широкую область применения. Часто их используют для повышения надежности прокладок, а иногда и вместо прокладок. В первом случае герметик наносят или очень тонким слоем или в виде очень тонкого валика диаметром 1–1,5 мм на обе стороны прокладки (рис. 20).

Рис. 20. Нанесение герметика
Герметику дают пару минут схватиться на воздухе, а затем собирают узел. В случае если герметик используется вместо прокладки (например, при уплотнении масляного поддона), герметик наносят на обезжиренную поверхность поддона в виде валика диаметром 5–6 мм без разрывов, и обходя дополнительно отверстия под крепеж (рис. 21).
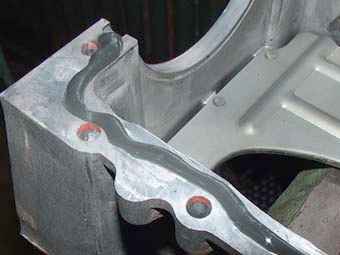
Рис. 21. Нанесение герметика на поддон
Герметику дают схватиться на воздухе в течение 10–20 минут, после чего поддон монтируют на обезжиренную поверхность блока и слегка притягивают болтами так, чтобы слой герметика почти полностью, но не до конца сжался. После этого соединение выдерживается полчаса- час и крепежные болты полностью затягиваются. Совершенно нелишним будет напомнить, что перед монтажом, прилегающий фланец поддона должен быть отрихтован до идеального прилегания, ибо ни один герметик не предназначен для компенсации халтуры.
Эластичные герметики применяют для соединений, которые приходится часто разбирать (например, для обслуживания) или просто для повышения надежности обычных прокладок. Часто эластичные герметики выпускаются в аэрозольной упаковке. Наиболее частое применение эластичных герметиков — соединение стыков и дополнительное усиление пробковых прокладок.